Introduction Job sites are complex ecosystems where efficiency is often compromised by...
Streamlining Stock Tracking: Techniques for Faster Movement
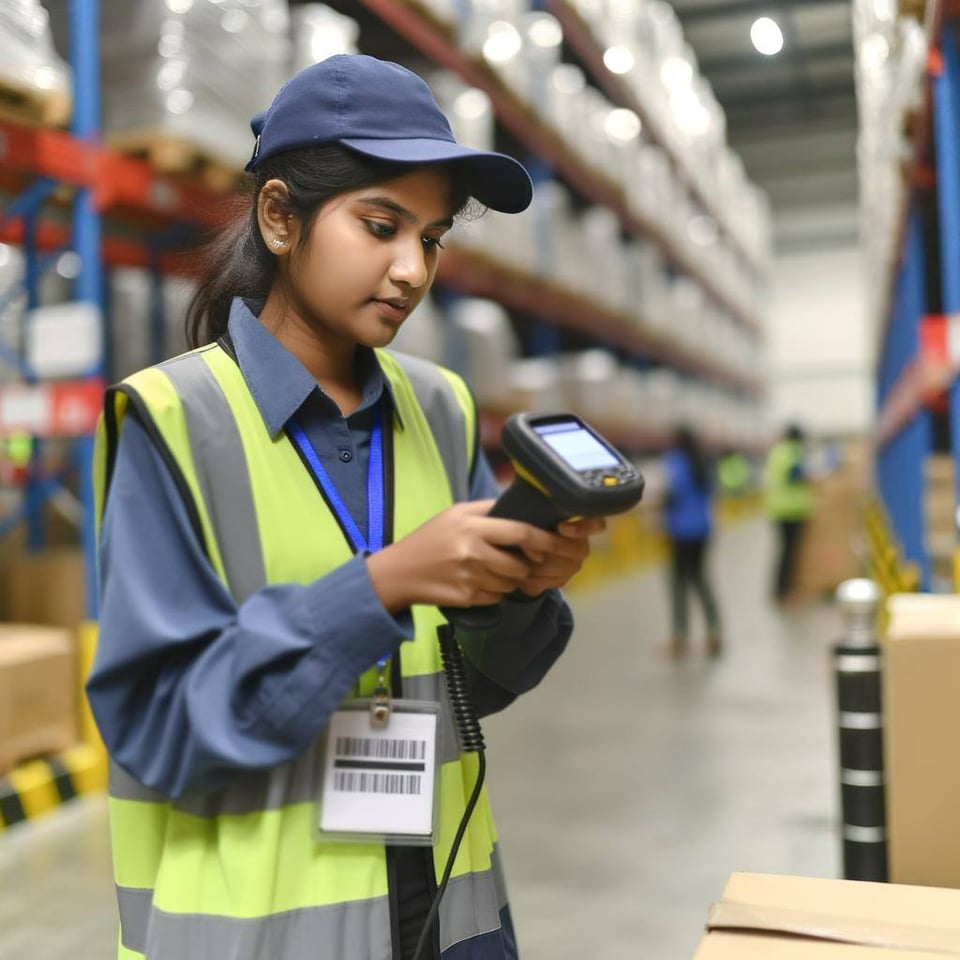
Discover how optimizing order picking processes can significantly boost warehouse efficiency and customer satisfaction.
Understanding the Basics of Order Picking
Order picking is a critical process in warehouse operations that involves selecting items from inventory to fulfill customer orders.
Efficient order picking is crucial for ensuring fast and accurate order fulfillment, which leads to improved customer satisfaction.
There are different order picking methods, including batch picking, zone picking, and wave picking, each with its own advantages and considerations.
By understanding the basics of order picking and selecting the most appropriate method for your warehouse, you can streamline the process and enhance efficiency.
Innovative Item Picking Technologies
To optimize order picking and improve warehouse efficiency, warehouses can leverage innovative item picking technologies.
These technologies include automated storage and retrieval systems (AS/RS), which use robotic systems to retrieve items from designated locations in the warehouse.
Another technology is pick-to-light systems, which use light indicators to guide order pickers to the correct locations and quantities of items to pick.
By implementing these technologies, warehouses can reduce picking errors, minimize travel time, and increase overall picking speed, resulting in faster fulfillment and improved customer satisfaction.
Furthermore, using these technologies can help warehouses handle items that are used in manufacturing processes, ensuring timely availability and avoiding delays.
Strategies for Layout Optimization in Warehouses
An optimized warehouse layout is crucial for efficient order picking.
By strategically organizing product locations, warehouses can minimize travel time and improve order picking productivity.
Some strategies for layout optimization include using ABC analysis to categorize products based on their demand and assigning storage locations accordingly.
Warehouses can also implement cross-docking, a method that eliminates the need for storage by directly transferring incoming goods to outgoing orders.
Additionally, implementing a slotting optimization system can help warehouses determine the most efficient storage locations for each SKU based on factors such as demand and product characteristics.
By applying these layout optimization strategies, warehouses can streamline order picking processes and enhance overall efficiency.
Managing Workforce Schedules
Efficiently managing workforce schedules is essential for optimizing order picking processes.
By tracking and reporting overtime and cost by shifts, warehouses can ensure that the workforce is properly allocated and avoid unnecessary expenses.
Implementing workforce management systems can help warehouses streamline scheduling processes and ensure that the right number of workers with the necessary skills are available during peak demand periods.
Furthermore, providing adequate training to new employees and regularly updating staff skills can contribute to improved order picking efficiency and overall warehouse performance.
Measuring Success: Key Performance Indicators
In order to assess the effectiveness of order picking optimization efforts, warehouses can utilize key performance indicators (KPIs).
KPIs such as order cycle time, order accuracy, and productivity can provide valuable insights into the efficiency of order picking processes.
Consumer goods companies, in particular, need to respond quickly to changes in demand, making it crucial to monitor KPIs and continuously improve order picking performance.
By measuring and analyzing these KPIs, warehouses can identify areas for improvement and implement strategies to further enhance order picking efficiency.